How Manufacturers Can Achieve Maintenance Excellence in Times of Constrained Resources
Key points:
- Order books remain filled, but concerns about lack of growth, especially in Germany, inflation, energy costs, supply chain, and recruitment issues continue to dominate boardroom discussions
- Rising interest rates dampen credit-financed investments
- Machinery producers are looking for new ways to accelerate full capacity recovery and generate productivity increases
- Increased reliability and uptime expedites response times and agility in responding to changing market demands, resulting in customer satisfaction and improved bottom-line results
- Maintenance is sometimes overlooked, yet a vital component in rapid improvement
- A&M's rapid diagnostic and transformation approach combines hands-on experiences, coupled with data analysis techniques
European machinery industry associations are expecting production outputs to continue growing throughout 20231, despite orders easing off. This unusual situation is reportedly caused by strong backlogs from last year and slowing demand for investments in new machinery as interest rates continue to rise.
This now begs the questions of how to effectively manage capacity, deliver on time and prepare for uncertain growth in an environment of higher raw material prices, persistent supply chain issues and challenges in recruitment. The industry today employs 10% less people than it did in 2019.
Many industry players are working actively on initiatives to attract and retain talent, for example by adopting flexible working beyond retirement age and enhancing the appeal of apprentice schemes. Mechatronic and automation-related workers are in short supply and a significant number of vacancies for apprenticeships in Germany remained unfilled in 2022, according to trade associations, and thousands of craft apprenticeships are still open today.
The challenge ahead is to tackle the near-impossible – producing more with less.
Many of our clients have looked inwards to free up hidden capacity and modernise operations. We have observed two main trends:
Firstly, a systematic focus on machine downtime, addressing root causes and using the additional capacity to bring down the cost of goods sold. One way to achieve this is to treat maintenance as a core value-adding process, not a separate function, as well as deploying cross-functional teams of operator-maintainers and investing in people (see Illustration 1).
Illustration 1:
This graph explains the type of activities of production operators and technicians before and after a maintenance transformation, showing the impact of both autonomous maintenance and professional maintenance on increasing the value-added time.
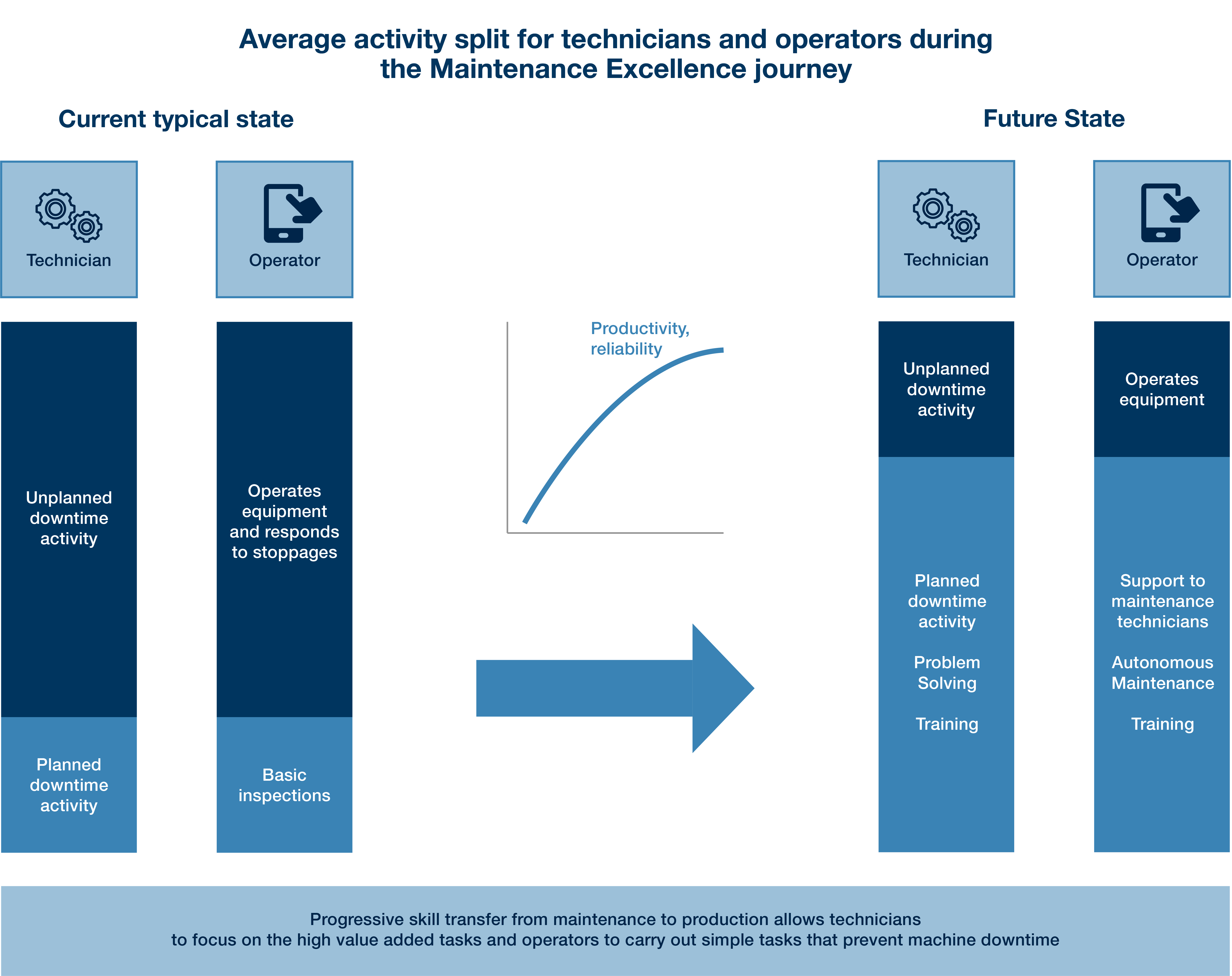
With cost pressures building up and skills in short supply, manufacturers have to think beyond simply adding shifts or using overtime.
Initiating a reliability transformation and driving change in maintenance practices can typically bring visible sustainable benefits after 10 to 14 weeks. Effective maintenance must be a continuous top management priority in times of constrained resources.
Secondly, companies are becoming more digital-savvy and bringing together operational data to systematically increase the transparency of performance and enable root-cause analysis of deviations. We often find operational performance data being collected, but not fully exploited. Integration of systems, for example, by putting a more user-friendly reporting tool onto the data from a Manufacturing Execution System (MES), leads to a performance boost, as supervisors are able to see trends and define actions with cross-functional teams.
Condition-monitoring and predictive maintenance solutions are becoming increasingly affordable with initial investment costs for a proof-of-concept no longer proving prohibitive.
A&M’s approach to improved productivity in maintenance is anchored in two principles:
- The proven methodologies that set the foundations for performance increase, with a focus on strategy, planning, execution and supporting technology.
- The selective adoption of already available in-house data to develop actionable insights using digital analytical tools.
For example, the first step of our diagnostic activity will be to run a data scanning module fed with historical data from quality, maintenance, production and machine automation systems such as MES, Quality Management System (QMS), Computerised Maintenance Management System (CMMS) and Supervisory Control and Data Acquisition (SCADA).
The second step is to identify, based on the data download, patterns or correlations between machine stops and maintenance activities, good candidate equipment for predictive monitoring (see Illustration 2), spare parts candidate references for improvement on availability and working capital reduction opportunities.
Illustration 2:
This illustrates the equipment condition decreasing with time, from developing failure to equipment stoppage. The remote condition monitoring and applied analytics allow it to generate a work notification with enough time ahead to plan the repair, thus making it much more efficient as a planned downtime and avoiding longer unplanned machine downtime and repair.

Organisations see performance increases ranging from 20% to 50% in direct labour productivity, typically after four to six months. Asset unplanned downtime is reduced towards top-quartile industry performance, depending on asset condition. In addition, enhanced transparency and predictability of work improve staff engagement, as well as management’s ability to reward the newly adopted behaviours.
A&M can help you create short-term results in your facilities, by taking the additional step, through a focus on downtime and targeted problem-solving. In parallel, we can also support you to build the foundations for sustained success through equipment and asset strategy, organisational model, work processes, CMMS, and digital innovation.
Increased uptime and reliability create additional capacity – first in larger, then in incremental steps – and this is directly transferable to productivity. Companies can therefore optimise their scarce people resources, dedicating their talent towards more value-add activities including client projects and R&D, and less on repetitive tasks such as repairs.
What’s more, we often witness improved levels of employee satisfaction due to better productivity and business performance.
If you are interested in learning more please contact Roswitha Tertea, Alex Krause or Romain Vallee.
1 The German Machine Tool Builder’s Association (VDW) expects 9% growth in 2023, which was mirrored by the European Association of Manufacturing Technologies (CECIMO).
References: