THE ROAD TO INDUSTRY 4.0 SERIES (PART 1) – TECH AND DIGITAL TECHNIQUES IN INDUSTRIAL SETTINGS
Part 1: Overcoming Challenges in Legacy Manufacturing Systems
Making the move to Industry 4.0 can seem daunting for many manufacturing organisations. It involves moving away from decades-old legacy systems that are not only highly complex but also critical for the day-to-day operations of the business. Reconfiguring, modifying or replacing major applications can be cumbersome and expensive, as well as hugely disruptive to the business operations.
However, it is possible for companies to upgrade legacy applications and IT infrastructure to obtain the benefits of Industry 4.0, in an incremental and cost-sensitive way. In the first instalment of our Digital Manufacturing series, we explore some of the techniques being deployed by A&M’s experts to deliver rapid solutions to the real-world problems of clients.
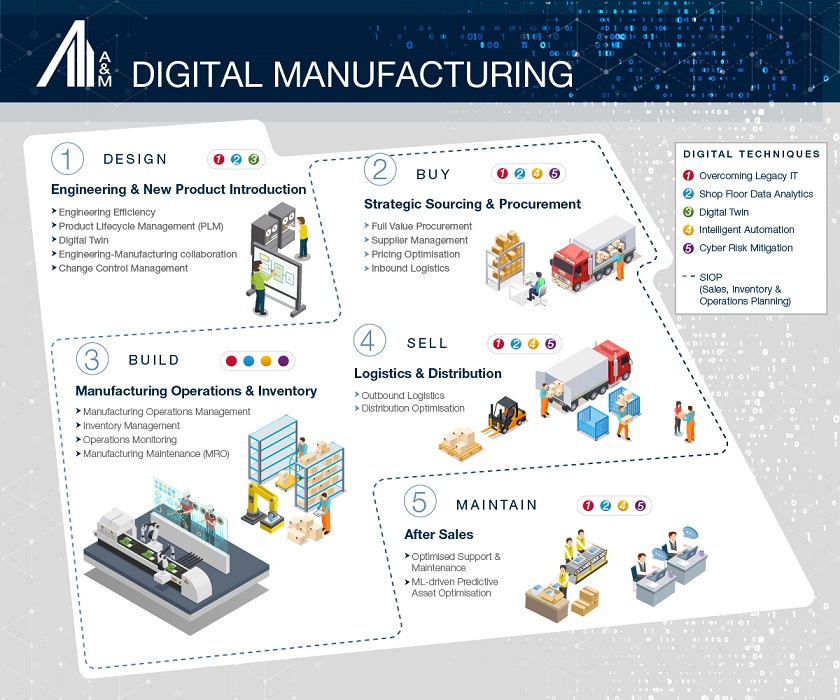
1. Embrace Robotic Process Automation (RPA) for efficiency and improved data insights
In a shop floor environment, operators need to periodically collect data for time recording, quality checks or productivity reports, among other compliance and business intelligence needs.
This information is often locked in disparate legacy systems, with little to no integration between them. This makes data gathering and analysis too dependent on manual labour, and therefore time-consuming and costly.
RPA technology can bring speed and efficiency to these repetitive, labour-intensive tasks. Unlike humans, software robots can work across different systems to process and analyse large volumes of data in an error-free, consistent manner.
Critically, these tools allow for rapid deployment and – contrary to general perception – have reasonable implementation costs. Not only can they be integrated with existing legacy systems without expensive software development, but measurable results can be achieved within months of implementation.
Major RPA use cases in industrial environments vary from back-office processes (invoice processing, inventory management) to core manufacturing operations (data recording and processing associated to quality, maintenance, regulatory compliance or forecasting activities, among others.)
RPA can also be combined with other technologies such as artificial intelligence (AI) and advanced analytics to identify patterns within the data and provide insights and predictions about the future.
For example, data insights into production machine performance can help engineers optimise their maintenance plans, taking action before failures happen and avoiding unplanned downtime, which can cost industrial and manufacturing companies hundreds of millions of dollars annually. Centralised data is also beneficial for improvement initiatives, as it enables manufacturing operators to quickly spot variances in processes and outcomes between production lines, sites, divisions and locations.
Based on A&M’s recent work with manufacturing clients, benefits of RPA and other intelligent automation processes include a 30% to 40% improvement in labour productivity on average, as well as a 10% to 20% reduction in machine downtime and overall maintenance costs.
Whilst investing in RPA has been proved to generate significant improvements in ROI, businesses should also be realistic about the need for constant upgrade and maintenance as industrial processes evolve and new products are added to the shop floor. Therefore, we estimate that 15% of the initial gains can be absorbed into annual recurring costs required to update and keep RPA relevant.
2. Break down the data silos
In manufacturing and industrial environments with a high dependency on legacy systems, engineers and administrators can spend a significant share of their working hours hunting down information across different databases and systems that are poorly integrated and often isolated from one another.
A variety of modern digital capabilities can help companies to eliminate these data silos, enable them to collect and make sense of proprietary operational data like never before. One technique is data virtualization, which allows organisations to retrieve and manipulate data from heterogenous sources without replication – that is, without moving the data to a physical repository. It does that by adding a virtual layer on top of the legacy data source (also known as “digital decoupling”), enabling data users to access it in real time regardless of its format or location.
This approach does not require large infrastructure and excessive implementation costs, offering a cheaper and faster alternative to data warehousing. There is also the benefit of enhanced security and more consistent data governance resulting from the centralised data architecture, in addition to greater flexibility, scalability and faster deployment.
A strategy for improved data governance must be implemented alongside an approach for business process integration.
A focus on the application architecture, including how critical systems are integrated and how common data is shared across them is key. Among multiple tools and methodologies designed to improve application integration, the use of Application Programming Interfaces (APIs) is a common approach. APIs can be used to define the most critical applications in a large legacy application portfolio and ensure that they are communicating with each other. This can be used to enable process efficiency and consistency as well as driving improved data quality and overall process effectiveness.
3. Adopt hybrid cloud to enable agile innovation
Cloud-based computing is a key enabler of Industry 4.0 and 5.0 technologies. However, many manufacturing leaders may be sceptical about moving critical operational data to third-party cloud service providers due to concerns around security, latency or resiliency.
One common approach for manufacturing businesses facing this dilemma is to mix on premise, private cloud and public cloud services with orchestration between them, a so-called hybrid approach. It provides the agility and flexibility needed to innovate within a legacy environment, without compromising on quality or security.
This approach also helps accelerate deployment in a large multi-site or multi-country scenario, as changes made within the newly introduced cloud services in a legacy environment can be quickly rolled out to other plants and countries.
This can be particularly valuable for companies looking to modernise their IT stack in line with Industry 4.0 solutions. For example, if a new application is being tried out, public cloud resources can be allocated to trial the solution, and only incorporated into the portfolio if and when the technology has been proven.
Cloud-based systems offer manufacturing companies faster upgrades, ensuring their software is protected from security vulnerabilities and automatically updated to new features. Because the data is stored in offsite servers with stringent security standards in place and several layers of redundancy, companies can expect stability issues to be less prevalent compared with on-premises infrastructure.
Stay tuned for more on shop floor data analytics, digital twin and cyber risk mitigation
This is the first part in our series of articles looking at the digital techniques that are helping companies to reduce cost and improve efficiency in industrial environments. Subsequent articles will focus on shop floor data analytics, digital twin technology, intelligent automation and cyber risk mitigation.
How can A&M help?
A&M has developed a comprehensive digital factory diagnostic model based on three key pillars: Leadership, Technology and Business Value. As part of this work, we have conducted Proof of Concept exercises and run pilot implementations which include large-scale, multi-site rollouts of the digital techniques highlighted in this article.
Our team of experienced operators and data scientists are equipped to help companies not only generate insights from existing data but assess, prioritise and roll out solutions at scale to achieve maximum return on investment, as quickly as possible. We work with clients to implement and train large teams, building strong business processes and decision-making that are complimentary to the new data and digital tools.
Contact us today to learn how A&M can tailor these ideas to your business objectives and deliver tangible, sustainable results.
A&M. Leadership. Actions. Results.
A&M Digital helps organisations unlock trapped value by bringing together the capabilities, technology and talent needed to incubate, launch and scale digital products, platforms, and businesses while reducing costs and creating efficiencies within your operations.
We provide end-to-end digital services that release the power of data and AI. Our approach helps businesses create amazing digital experiences, accelerate digital growth, modernise technology and automate operations. Our clients are empowered to generate and use actionable insights to build the digital talent and culture needed to win against the disruptions they face in their respective industries.
[1] https://www.automation.com/en-us/articles/june-2021/world-largest-manufacturers-lose-almost-1-trillion
[2] https://blog.isa.org/how-to-upgrade-legacy-equipment-for-an-industry-4.0-factory